Whitespot, Waterspot and Visually Fault-Free Prepreg for Composite Materials
Previously, the time-consuming techniques for manufacturing traditional composite materials made it not desirable for composite materials to satisfy the demand for matching curing time with the takt time found in the automotive industry. This, in turn, limited the deployment of the earlier generations of prepregs in automotive mass production and meant that composite use remained restricted tohigh-end segments. To solve this problem, Kordsa developed and introduced a carbon-look class-A surface giving CM11 resin and its prepreg system which was not just isothermally press-curable in underthree minutes at 150°C but also hot-demouldable, thus yielding an ideally suited system to the needs of the automotive industry.
In the automotive industry, the demand for visually-appealingcarbon-look composite parts continues to grow. The resin systems usedin prepreg materials include different epoxy resins, curing agents,catalysts and performance/process-improving additives. Transparentand colorless epoxy resins, curing agents, catalyst and additives are chosen in the manufacture of carbon-look prepregs to improve visual apperance. However, while the composite part may be transparent immediately after demoulding, environmental conditions, UV-exposure, heat/cold and humidity usually affect their visual appearance in time and may cause them to change colour and lose their gloss and transparency.
The use of latent amine curing agents in modern hot-melt epoxy prepreg materials brings the advantage of lower health risks forworkers compared to the use of boron- and anhydride-based curing agents. The drawback of latent amine curing agents, however, is thatwhen dicyandiamide (DICY) in particular interacts with humidity and CO2 in the atmosphere or is exposed to other types of environmental influences, the result may be the problem commonly called white wash,water spot or white spot.
There are five potential causes of white spot, water spot and similarlywhite/opaque apperances (which commonly many types of surfacedefects are confused with white spot although their mechanism is different however the appearance of fault is very similar and veryundesirable):
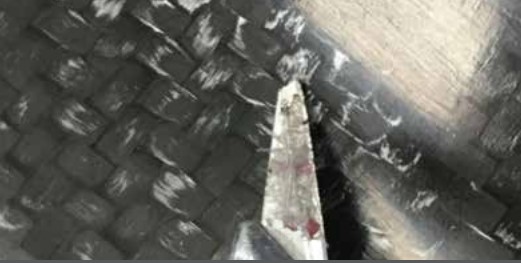
Figure 1: Carbon look composite part following incidence of white spot due to exposure to humidity.
- Opaque tougheners or additives with a large particle sizes (such as fillers or silica) accumulate in certain regions and precipitate out from the resin mixture during cure (although this problem is unrelated with white spots the end result can be very similar in appearance).
- When excessive amounts of solid curing agents or catalyst pastes are used in epoxy or the resin flow is too high, these agents or pastes filter out from the fibers and then excess solid curing/catalyst agents precipitate.
- The curing cycle when it is not sufficient to melt the solid curing agent/catalyst (wrong choice of curing cycle) so it can react with epoxy; because of this, solid curing agents and catalysts may appear as white spots.
- Epoxy resins by nature have a low resistance to heat cycling/humidity and UV. If the resin flow is too high or the resin content of the prepreg is low for the specified curing cycle parameters then in turn on the surface of fibers, the resin layer will be too thin to protect the fiber-epoxy interface from being harmed by humidity, heat and/or UV.
- The epoxy/curing agent/catalyst system contains additives or components with high hygroscopicity; upon exposure to water or high humidity levels, the surface of the epoxy film absorbs water and the fiber/epoxy interface is then harmed.
Kordsa was determined to eliminate water spot or similar colour-inhomogeneity problems from its new hot-melt epoxy prepregmatrix. Its new generation resin systems contains no silica, fillers,coloured toughener or coloured additives. Also, the new resin system exploits new UV-absorbers and anti-oxidants which do not change their colour, neither from transparent to opaque nor from colourless to coloured. Since Kordsa prioritises the health of its workers andcustomers, it decided not to use any harmful anhydrides orboron-containing curing agents. Kordsa’s new approach involves thecareful calculation of resin matrix epoxy/curing agent/catalyst stoichiometry and the optimisation of the curing cycle to enable itscustomers to benefit from the maximum degree of cure. Kordsa has designed its own composite matrix from scratch and created a unique resin formulation, a new generation fast-press curable resin called CM14 and its autoclave curable counterpart OM15, which eliminate waterspot and whitespot problems, thus providing high visual clarity.
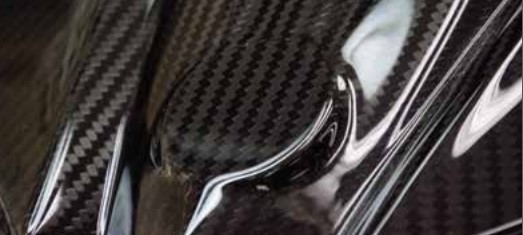
Figure 2: Composite part made with waterspot/whitespot-resistant CM14 resinsystem containing prepreg.