The Potential Applications of Carbon Fiber in Tire Technology
15 November 2016
Sadettin Fidan
IP and Technology Manager, Tire Technologies
In tire technology, the principal property requirements for each of the main tire reinforcement components can be summarized as follows:
BEAD RING: Ultra high modulus, high strength and high bending stiffness
BODY PLY: High strength, dimensional stability and fatigue resistance
BELT PLY: High strength, ultra-high tensile modulus and axial compression resistance C
AP PLY: High modulus, medium heat-shrinkage, and high thermal contraction force
Carbon fiber (CF) has exceptional tensile modulus, strength and dimensional stability properties, but has certain shortcomings in soft rubber matrix of tire applications. The primary solution parameter to overcome this problem in soft matrix applications seems to be polymeric or resinous fillers, which improve stress-transfer uniformity and abrasion resistance between stiff carbon filaments. The potential tire applications of CF-based reinforcements can be given as follows:
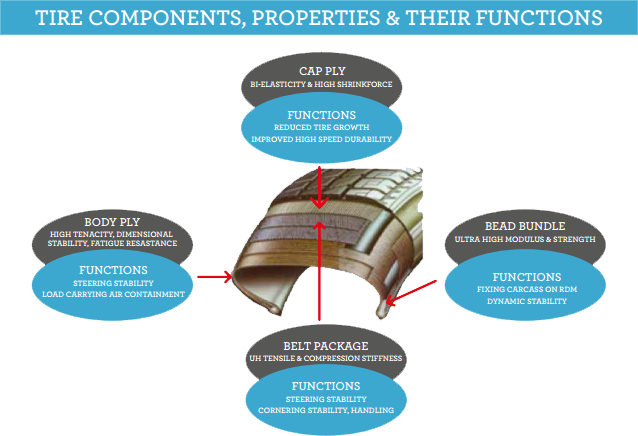
TREAD
As an ingredient in tread compound, either as powder or dipped chopped fiber (DCF), carbon fiber improves not only electrical conductivity to enable static electrical discharge from the tire to the road contact surface with the footprint, but also shortens the dry and wet braking distances by means of the spiking effect of the sharp ends of the fibers on the road surface. In order to reduce rolling resistance and heat build-up in the crown area, while the low carbon black and high silica content reduce tread conductivity, the carbon fiber, as a powder or DCF, also improves the electrical and thermal conductivity and additionally contributes to enhanced heat dissipation.
BEAD WIRE/CORE
High-strength, ultra-high modulus single-twisted CF strands can function as perfect bead wire due to the capability to maintain their original physical properties. The original modulus and strength can be maintained by controlling inter-filamentary stress transfer with polymers filling yarn-bundle interstices. The first potential candidates for such applications are racing and high speed tires. Different strength and stability levels can easily be obtained by adjusting the number of windings of 6K or 8K CF strands in the bead core. Polymeric or resinous fillers/matrices could increase the breaking elongation of up to 4-5% with some helix configurations. The most important motive for this application is weight reduction and fuel saving.
SIDEWALL INSERT & SIDEWALL REINFORCEMENT
In order to improve the run-flat performance and to decrease the heat build-up, CF cords can be applied as a sidewall reinforcement, or CF short fibers and powders can be applied as an ingredient in the sidewall insert rubber. Such measures can increase the radial stiffness and decrease sidewall deflection under reduced inflation pressure. Increased thermal conductivity also helps reduce the temperature rise, which improves run-flat driving performance.
BEAD REINFORCEMENT
With a tensile modulus higher than 15,000kg/mm2, CF cords have been used as bead reinforcement in radial tires to improve high-speed steering stability and to provide comfort. Full RFL(or similar adhesive systems) penetration into filaments is a must for improved bending-fatigue resistance. Cord-twist optimization is necessary to hold the filaments tightly together, because of the negative effect of high twist on cord strength and modulus.
BELT PACKAGE
CF-cord reinforcement, as a folded belt package with or without cap ply, improves high-speed durability by preventing early belt-edge separation that leads to tire failure. While ultra-high modulus CF enhances the circumferential tensile stiffness , the out-of-plane flexibility of the belt layers provides reduced radial stiffness and more comfort compared to conventional tires with steel cords as a belt. Furthermore, with the low specific density of CF,tire weight and rolling resistance can be reduced.
In order to increase belt-cord integrity and its performance under dynamic conditions, full impregnation of the CF bundles in twisted or non-twisted form with thermoplastic, semi-thermoplastic or thermoset resins might be necessary. This treatment increases cord compression, bending and cut resistance. As a result of cord compactness, resistance against surface-filament separations under shear conditions is improved.
When compared with steel, aramid and glass, CF can generate less stress/strain concentration at the belt edge zone. Cornering stiffness can be controlled with cord compressibility,angle with the equatorial plane, end count and linear density.
Another potential application of stiff CF elements can be in the cut-end cross-angled belt package.
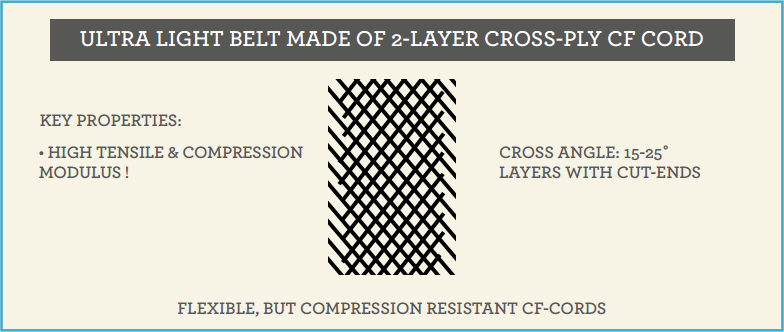
CAP PLY
Theoretically, CF cords, with a breaking elongation of lower than 2.0%, can not be used as spirally wound cap ply due to the lifting of the belt package during the tire curing process, which could lead to the belt compound being penetrated by the CF cords and the friction between the CF cords and steel cords under high tension. Under such process conditions, low-extensible CF cords can be broken during lifting (tire expansion).
For these reasons, Kordsa Global is developing bi-elastic CF strips with a breaking elongation higher than 4% and with a tenacity/strength at least three times higher than conventional CF cords by applying a special axial relaxation process. Such CF reinforcements as spirally wound cap ply strips on belt package prevent tire growth and pantographic belt-edge movements under high-speed conditions. Such bi-elastic CF strips also have exceptional cut-resistance against FOD (Foreign Object Damage).
In summary, CF-based reinforcing cords, strands and strips could open new horizons in tire applications, if prepared under the proper conditions with tailor-made properties.
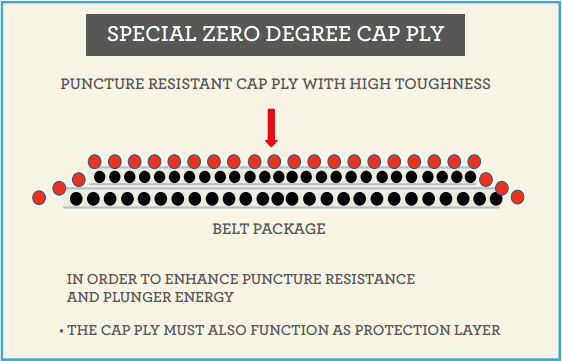