Process-Induced Residual Stresses In Polymer Composites
17 June 2020
Dr. Fatih Ertuğrul ÖZ
Tags :
1. Introduction
This article presents process-induced residual stresses and their distorting eGects in the manufacture of thermosetting polymer composites. It shows the eGect of the diGerent properties of constituents, how they develop during the cure cycle, and how they cause cure shrinkage that results in residual stresses at the micro level and manufacturing distortions at the macro level.
2. DiGerent thermomechanical properties Advanced composite materials for structural applications make use of high performance fiber reinforcements such as the carbon fibers in thermosetting polymer matrix materials. Both have diGerent mechanical and thermal characteristics. A comparison of the physical properties of a type of carbon fibre with those of an epoxy matrix is given in Table 1.
As the table indicates, the elastic modulus of carbon fibre is almost 60 times higher than that of epoxy. In addition to this, carbon fibre is an othotropic material, whose mechanical properties are not
the same in all directions. A similar situation applies to thermal expansion coeficients. Moreover, the thermal expansion coeficient of carbon fibre is negative in a longitudinal direction. This means that, when exposed to a temperature gradient, carbon fibre behaves the opposite way to epoxy.
Mismatch in thermal expansion coeficients is the most important factor behind thermal residual stresses throughout the cure cycle.
3. Cure Cycle Of Composite Materials
Advanced composite products are manufactured through the consolidation of pre-resin impregnated fibres (prepregs) in autoclave. This consolidation is achieved through applying high temperature and pressure. During cure development, the resin undergoes various changes. An example of the cure cycle of an epoxy resin is shown in Figure 1. It can be summarized as follows [1, 2]:
- The blue lines represent the applied temperature, while the red markers show the development of the elastic modulus of the resin throughout the cure cycle.
- The elastic modulus is initially zero. Then it starts to develop when the temperature reaches the gelation point, which is on the second ramp.
- When the temperature reaches glass transition temperature during the second plateau, the rubber-like resin starts to turn into a solid material.
- Finally, at the end of the cooldown, the resin reaches its elastic modulus value in Table 1.
Figure 2 shows the through-the-thickness cure shrinkage of the unidirectional (UD) laminates throughout the cure cycle. Figure 2 can be summarized as follow [1, 2]:
- Prepregs experience thermal expansion and shrinkage during the first step (heating up to the first plateau) and the last step (cooldown) respectively.
- Consolidation becomes dominant during the first plateau, and the resin starts to shrink non-linearly.
- Then, thermal expansion competes with cure shrinkage during the second ramp.
- The resin expands until the gel point, after which cure shrinkage overtakes thermal expansion. Finally, consolidation occurs as a result of thermal shrinkage during cooldown to room temperature.
The aforementioned mechanisms throughout the cure cycle result in residual stresses and give rise to manufacturing distortions at the end of the cure cycle.
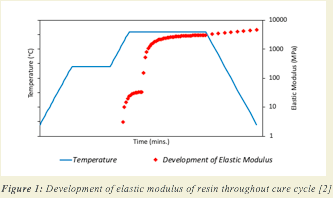
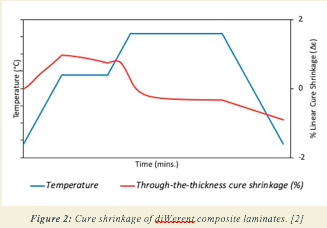
4. Development Of Residual Stresses In Composite MaterialsResidual stresses are the stresses that remain in a material or structure after the source of these stresses has been removed. They can be caused by the application of external mechanical or thermal loads. While the former can be due to plastic deformations, the latter can be due to thermal gradients in a high temperature process.
Residual stresses in composites are classified into two categories: micro- and macro-residual stresses. Micro-residual stresses develop at the level of the constituents due to the diGerence in the thermal expansion coeficients and the cure shrinkage of resin, which may have an adverse eGect on the mechanical properties of the final product due to fiber-matrix debonding. On the other hand, macro- residual stresses occur due to the interaction between plies and the mold material. They take place in the laminate and result in shape distortions after manufacturing.
A numerical, finite-elements model was developed to calculate the process-induced micro-residual stresses in carbon fibre-reinforced epoxy composite material [2]. The geometry of the model is a simple representative volume element, in which the fibers are distributed inside the resin in a hexagonal array, as shown in Figure 3. The circular regions in Figure 3 represent fibers and the remaining parts in the rectangle represent epoxy resin. The constant mechanical properties in Table 1 stand for carbon fibre, whereas the developing elastic properties in Figure 1 are associated with the epoxy resin. In addition to this, the model incorporates linear expansion/shrinkage variation throughout the cure cycle shown in Figure 2.
Since the strain variation in Figure 2 occurs as a result of chemical reactions and thermal gradients, residual stresses accumulate throughout the cure cycle and remain within the fibres and matrix at the end. Figure 4.a shows that there are tension (67.74 MPa) residual stresses in the matrix and compressive (-47.5 MPa) residual stresses in the resin. When a detailed examination is carried out
in Figure 4.b of the resin, the regions where the fibres are closest to each other appear to display the lowest stress, whereas the fibre
resin intersection regions, in which the fibres are furthest from each other, exhibit the highest tension residual stresses. This indicates that fibre/matrix debonding will be initiated from this region when a part is exposed to subsequent loading. The compressive and tension residual stresses in the fibres and resin are balanced with respect
to the fibre volume fraction (59%) of this composite material at the micro level, as shown below:
67.74 ·(1-0.59)-47.5·0.59=0 (1)
When UD prepregs are laminated and laid onto a mold, mechanisms due to tool-part interactions are activated, and this brings about macro-level residual stresses which lead to distortions in parts. They can be seen in a U-shape mold, as in Figure 5. The mechanisms causing these distortions can be summarized as follows [3]:
- When the tool and part are forced together through autoclave pressure and subjected to an increase in temperature, a shear interaction occurs between the tool and the part due to the fact that the metal and the composite have diGerent thermal expansion coeficients.
- As this occurs prior to any significant degree of resin modulus development, the laminate modulus is very low and plies that are distant from the tooling are not loaded to the same extent as those close to the mold.
- This non-uniform stress distribution is locked in as the resin cures, and once the tooling is withdrawn.
- The resulting bending forces the part to fold away.
A macro-scale finite element model was developed to simulate the curing of 4-plies UD laminate on a U-shaped mold to see the resulting distortions at the end of the cure cycle [3]. The cure
shrinkage and elastic moduli developments in Figure 1 and Figure 2 were applied to this model. The predicted manufacturing distortions at the end of a U-shaped part’s cure cycle are presented in Figure 6. The resulting spring-in is evident. The magnitude of distortions is around 3 mm from both ends of the molds. The actual measurements of the manufacturing distortions of a real U-shaped part at the end
of the cure cycle can be seen in Figure 7. The measurements are very close to the predicted values. Residual stresses always form in the composites and cause distortion. However, they should be
considered during the design phase of the parts and the shape of the molds should be designed with an eye to the desired final shape of the products at the end of the cure cycles.
5. ConclusionThe manufacturing of composite materials is a high temperature process in which two constituents with diGerent mechanical behaviours are processed together. This mismatch is an inevitable attribute of composite materials and gives rise to diGerent mechanisms throughout the cure cycle, causing the formation of residual stresses and shape distortions in final products. Process- induced residual stresses in composite materials are unavoidable, but they should be taken into consideration in both the design and manufacturing process in order to meet the twin requirements of dimensional accuracy and good property performance.
6. References
1. N. Ersoy, T. Garstka, K. Potter, M. R. Wisnom, D. Porter, M. Clegg, and G. Stringer, “Development of the properties of a carbon fibre reinforced thermosetting composite through cure”, Composites Part A: Applied Science and Manufacturing, Vol. 41, No. 3 pp. 401–409, 2010.
2. F. E. Öz, K. Cinar, and N. Ersoy, “Micromechanical progressive damage model for predicting resin dominated strength values of fibre reinforced composites under various types of loading”, ECCM 2012 - Composites at Venice, Proceedings of the 15th European Conference on Composite Materials, No. June pp. 24–28, 2012.
3. K. Çınar, N. Ersoy, and F. E. Öz, “3D process modelling for distortions in manufacturing of polymer composite materials,” ECCM 2012 - Composites at Venice, Proceedings of the 15th European Conference on Composite Materials, 2012.