Kordsa is Participating in the EU-funded Horizon 2020 Project “Polynspire”
Kordsa is a participant in the European Union-funded Horizon 2020 Project “polynSPIRE” (Demonstration of Innovative Technologies towards a more Efficient and Sustainable Plastic Recycling, Grant agreement ID no. 820665), which started in September 2018.
Coordinated by CIRCE, the Research Centre for Energy Resources and Consumption (Zaragoza, Spain), polynSPIRE has a duration of 48 months (1st September 2018–30th August 2022) and a total budget of 9.95 million Euros. The EU contribution of the project is around 7.95 million Euros. The kick-off meeting of the project was held in Brussels, Belgium on 25th-26th September 2018.
Thermoplastic materials (PP, PE, PET, PA, etc.), which are based on fossil fuels, are used in a vast range of products and applications ineveryday life but also generate an ever-increasing amount of plastic waste. Even though, throughout Europe, significant attempts are made to recycle, landfilling, incineration and reusing are the preferred methods for handling plastic waste. In 2016, over 27 MT of plastic waste were collected for further treatment.
There are several technological and non-technological barriers to plastic waste recycling. One of the biggest technological barriers is the insufficiency of the current waste management system in terms of the separation of plastic blends and composites. The heterogeneity and variant structure of plastic wastes is another challenge for mechanical recycling. This makes it all the more difficult to process large quantities of different types of plastic waste so that they can be introduced into the value chain. Moreover, plastic waste is generated at different points along the value chain. Due to the diversity in consumption patterns and in standards across Europe (cf. waste directives and the “End of Waste Criteria”), it becomes harder still to map, classify and deliver plastic waste types.
The aim of the project is to develop novel strategies for sustainable and cost-effective recycling processes for post-consumer and post-industrial waste streams in which at least 80% of the contents are plastic materials. The consortium also aims to develop a comprehensive business plan, offering 7 business models and establishing a cross-linked relationship between the plastic, chemical and steel manufacturing industries (Figure 1)
Figure 1: polynSPIRE Business Plan
The project brings together 21 leading entities: 4 research & technology organizations, 1 university, 9 large companies, 5 medium-sized enterprises and 2 multiplier associations. The chemical companies are Kordsa (Turkey), Repsol Quimica (Spain), Nurel (Spain), Arkema (France) and Novamont (Italy). The plastic compounder is Bada (Spain), the converter Maier UK (United Kingdom) and the waste manager IdealService (Italy). The technology developers are CIRCE (Spain), Kemijski Inštitut (Slovenia), Ioniqa (Netherlands), AITIIP (Spain), Eindhoven Technical University (TU/e, Netherlands) and RINA Consulting (Italy). The equipment and steel manufacturers are Fricke und Mallah (FM, Germany), Chemical and PharmaceuticalProcess Engineering (CPPE, Slovenia), HTT Engineering (Czech Republic) and Ferriere Nord SPA (Italy). The Danish Standards Foundation (Denmark) is implementing standardisation while European Plastic Converters (EuPC, Belgium) and the Istanbul Chemicals & Chemical Products Exporters’ Association (İKMİB, Turkey) are responsible for dissemination
The overall objective of polynSPIRE is to propose a comprehensive setof innovative, cost-effective and sustainable solutions aimed atimproving the energy and resource efficiency of the recyclingprocesses for materials containing plastics. These solutions pertain toboth post-consumer waste, i.e. the waste generated when products havecome to the end of their lives, and post-industrial waste, i.e. aste generated during the transformation of raw materials into finalproducts. Achieving this objective depends on three innovation pillars, which are implemented in operational environments reaching TRL 7Figure 2):
Innovation A (Chemical Recycling): The aim of this pillar is to recover monomers (adipic acid and hexamethylene diamine in Kordsa’s case) and fillers (carbon fiber, glass fiber, minerals, etc.) from engineering plastics and thermoplastic composites. Essentially this means that plastic parts will be extracted from household, automotive, electrical & electronic (E&E) products. Afterwards, these plastic parts will be treated with microwave-assisted equipment, enabling an up to tenfold increase in the reaction rate while reducing energy consumption by 65%. Moreimportantly, the reaction yield is estimated to increase from 70% to 82%
The use of smart magnetic materials is another strategy for chemicalrecycling, yielding an increase in the conversion rate for the target polymers from 18% to 80%. This is also estimated to lower energy consumption, thus enabling an increase in energy eficiency of around 60%. One of the biggest advantages of this technique is that it makes it possible to work under milder reaction and process conditions.Removal of magnetic catalysts from the process and their recovery are also possible, thereby further reducing the environmental impact and the operational cost of the process.
Innovation B (Mechanical Recycling): The mechanical recycling pillar is comprised of different methods for enhancing the quality of recycled plastics, using vitrimers, high-energy radiation, and compatibilizing additives. These two innovative recycling approaches can lead to a 34% direct saving in fossil resources in the case of Polyamide (PA) and a32% saving for Polyurethane (PU).
Innovation C (Valorisation): Finally, the valorisation of plastic waste as a source of carbon could enable the steel industry to reduce its use of fossil carbon sources in electric arc furnaces (EAF) by around 80%.

Figure 2: General view of plastic recycling/valorisation strategies along the plastic value chain.
The project will reveal the optimal technical, environmental andeconomic fit for different materials, taking into account parameterssuch as waste source (post-industrial or post-consumer), composition, and contaminants. A Life Cycle Assessment (LCA) and Life Cycle Cost (LCC) of the different strategies will be executed in order to investigatethe economic and environmental advantages for each recycled material.
The project will deal with streams containing 100% waste and ensurethat at least 50% of the total plastics containing PA and PU is recycled, leading to a reduction in CO2 equivalent emissions of between 30 and 40%. The project also addresses non-technological barriers at EU level, such as issues of legislation and standardization, and proposes business models for integrating the aforementioned solutions into the overall plastic waste management system (Figure 3).
polynSPIRE will create a database by mapping the distribution of plastic wastes across Europe, with a focus on Polyamide (PA) and Polyurethane (PU) wastes, as well as these wastes combined with otherplastics such as Polyolefins (e.g. PE or PP). Additionally, the consortium will develop a guideline for overcoming potential legislative barriers. Six market sectors will benefit from the project,namely the automotive, appliances, electronics, construction, packaging and textile sectors.
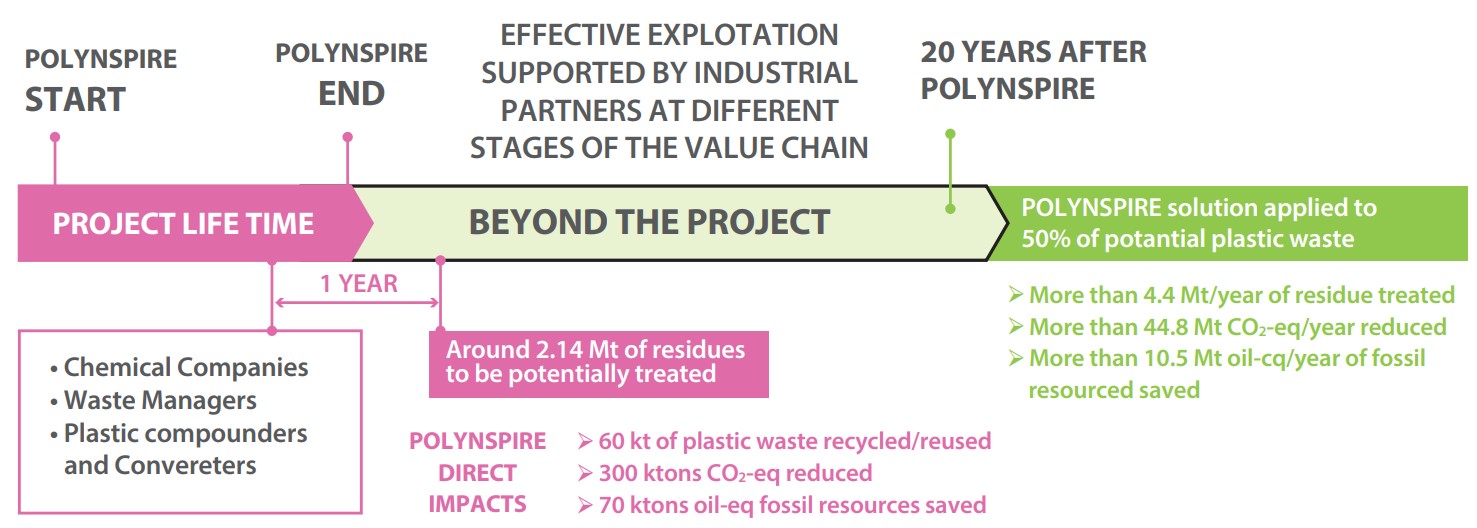
Figure 3: The expected impact of polynSPIRE.
Kordsa’s Contribution
As the Polyamide Validation Task Leader, Kordsa will be responsible for the validation of the recycled monomers for Polyamide-66 (PA66) and for fostering collaboration between Arkema (responsible for long-chain polyamides such as PA10, PA11 and PA12) and Nurel(responsible for polyamide-6).
The recycled monomers will reach Kordsa by means of the followingstages: (1) Plastic waste management and supply (PA66-based waste materials from several industrial products such as technical fibers and plastic parts); (2) Depolymerization of the polymers, extraction offillers/additives from the polymers and the purification of the recycled monomers (Figure 2).
Kordsa will develop new techniques for the polymerization of new rawmaterials. The usability of the new polymers that will be synthesized from the recycled monomers will be assessed by polymer users such as fiber producers, compounders and thermoplastic composites producers. In addition to conducting synthesis, Kordsa will performin-house compounding (engineering plastics) and lab-scale monofilament fiber processing of PA66. Depending on the wastesource, recycled raw materials may have different properties. This canpave the way to new polymer formulations and new products for themarket besides the standard PA66 polymer.
The project will have three main benefits for Kordsa. Firstly, it willallow the company to develop its know-how for new technologies and materials. Secondly, it will give Kordsa the chance to participate inshaping the business models of the future recycling industry. Finally, it will encourage the company to initiate new funded Horizon Europe projects, Horizon Europe being the successor research and innovationframework program to Horizon 2020.
References:
- https://www.polynspire.eu/
- https://polynspire.prezly.com/
- https://docs.wixstatic.com/ugd/81f3b1_6cf958f969bc4a279f6e41f4fd0635cb.pdf
- https://cordis.europa.eu/project/rcn/218601/factsheet/en
- https://www.spire2030.eu/